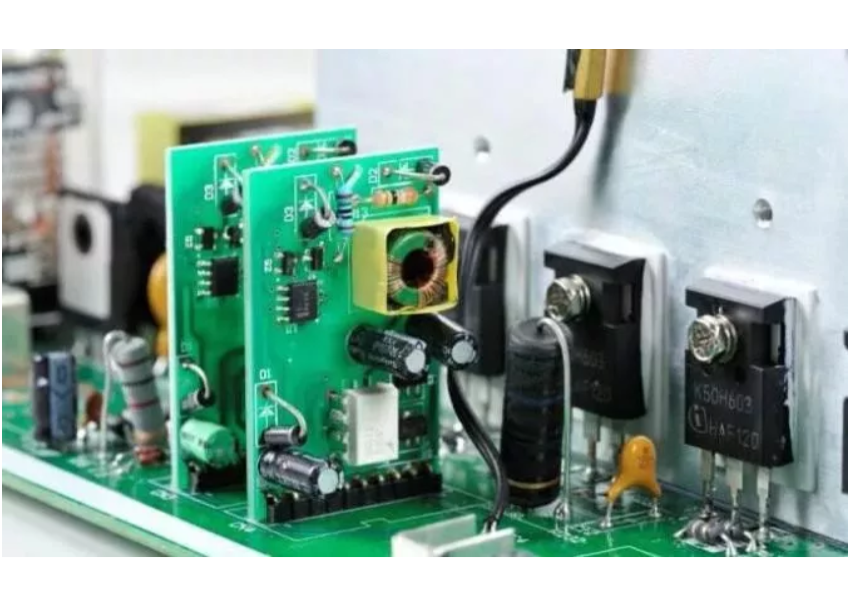
一、什么是灌封?
灌封(灌胶)就是将聚氨酯灌封胶、有机硅灌封胶、环氧树脂灌封胶用设备或手工方式灌入装有电子元件、线路的器件内,在常温或加热条件下固化成为性能优异的热固性高分子绝缘材料,从而达到粘接、密封、灌封和涂敷保护的目的。
二、灌封的主要作用?
灌封的主要作用是:
1)强化电子器件的整体性,提高对外来冲击、震动的抵抗力;
2)提高内部元件与线路间的绝缘性,有利于器件小型化、轻量化;
3)避免元件、线路的直接暴露,改善器件的防水、防尘、防潮性能;
4)传热导热;
三、3种灌封胶的优缺点?
1)环氧树脂灌封胶
环氧树脂灌封胶多为硬性,固化后和石头差不多硬,很难拆掉,具有良好的保密功能,但也有少部分为软性。普通的耐温在100℃左右,加温固化的耐温在150℃左右,也有耐温在300℃以上的。有固定、绝缘、防水、防油、防尘、防盗密、耐腐蚀、耐老化、耐冷热冲击等特性。常见的有环氧灌封胶有:阻燃型、导热型、低粘度型、耐高温型等。
优点:对硬质材料粘接力好,具有优秀的耐高温性能和电气绝缘能力,操作简单,固化前后都非常稳定,对多种金属底材和多孔底材都有优秀的附着力。
缺点:抗冷热变化能力弱,受到冷热冲击后容易产生裂缝,导致水汽从裂缝中渗入到电子元器件内,防潮能力差。并且固化后为胶体硬度较高且较脆,容易拉伤电子元器件,灌封后无法打开,修复性不好。
适用范围:环氧树脂灌封胶容易渗透进产品的间隙中,适合灌封常温条件下且对环境力学性能没有特殊要求的中小型电子元器件,如汽车、摩托车点火器,LED驱动电源、传感器、环型变压器、电容器、触发器、LED防水灯、电路板的保密、绝缘、防潮(水)灌封。
2)有机硅灌封胶
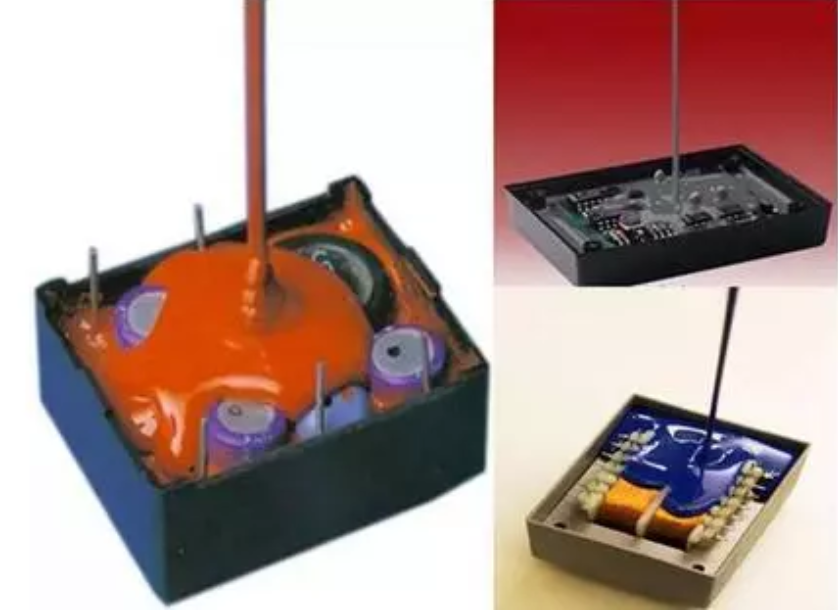
有机硅电子灌封胶固化后多为软性、有弹性可以修复,简称软胶,粘接力较差。其颜色一般都可以根据需要任意调整,或透明或非透明或有颜色。双组份有机硅灌封胶是最为常见的,这类胶包括缩合型的和加成性剂的两类。一般缩合型的对元器件和灌封腔体的附着力较差,固化过程中会产生挥发性低分子物质,固化后有较明显收缩率;加成型的(又称硅凝胶)收缩率极小、固化过程中不会产生挥发性低分子物质,可以加热快速固化。
优点:抗老化能力强、耐候性好、抗冲击能力优秀;具有优秀的抗冷热变化能力和导热性能,可在宽广的工作温度范围内使用,能在-60℃~200℃温度范围内保持弹性,不开裂,可长期在250℃使用,加温固化型耐温更高,具有优异的电气性能和绝缘能力,绝缘性能较环氧树脂好,可耐压10000V以上。灌封后有效提高内部元件以及线路之间的绝缘,提高电子元器件的使用稳定性;对电子元器件无任何腐蚀性而且固化反应中不产生任何副产物;具有优秀的返修能力,可快捷方便的将密封后的元器件取出修理和更换;具有优秀的导热性能和阻燃能力,有效提高电子元器件的散热能力和安全系数;粘度低,具有良好的流动性,能够渗入到细小的空隙和元器件下面;可室温固化也可加温固化,自排泡性好,使用更方便;固化收缩率小,具有优异的防水性能和抗震能力。
缺点:价格高,附着力差。
适用范围:适合灌封各种在恶劣环境下工作的电子元器件。
有机硅电子灌封胶相比其他灌封胶有什么优势?
优势1:对敏感电路或者电子元器件进行长期的保护,对电子模块和装置,无论是简单的还是复杂的结构和形状都可以提供长期有效的保护。
优势2:具有稳定的介电绝缘性能,是防止环境污染的有效屏障,固化后形成柔软的弹性体在较大的温度和湿度范围内消除冲击和震动所产生的应力。
优势3:能够在各种工作环境下保持原有的物理和电学性能,能够抵抗臭氧和紫外线的降解,具有良好的化学稳定性。
优势4:灌封后易于清理拆除,以便对电子元器件进行修复,并且在修复的部位重新注入新的灌封胶。
3)聚氨脂灌封胶
聚氨酯灌封胶又称PU灌封胶,固化后多为软性、有弹性可以修复,简称软胶,粘接性介于环氧与有机硅之间,耐温一般,一般不超过100℃,灌封后出现汽泡比较多,灌封条件一定要在真空下,粘接性介于环氧与有机硅之间。
优点:耐低温性能好,防震性能是三种之中最好的。具有硬度低、强度适中、 弹性好、 耐水、 防霉菌、 防震和透明等特性, 有优良的电绝缘性和难燃性,对电器元件无腐蚀,,对钢、铝、铜、锡等金属, 以及橡胶、塑料、木质等材料有较好的粘接性。
缺点:耐高温性能较差,固化后胶体表面不平滑且韧性较差,抗老化能力和抗紫外线都很弱、胶体容易变色。
适用范围:适合灌封发热量不高的室内电器元件,可使安装和调试好的电子元件与电路不受震动、腐蚀、潮湿和灰尘等的影响,是电子、电器零件防湿、防腐蚀处理的理想灌封材料。
四、选用灌封材料时应考虑的问题?
1)灌封后性能的要求:使用温度、冷热交变情况、元器件承受内应力情况、户外使用还是户内使用、受力状况、是否要求阻燃和导热、颜色要求等;
2)灌封工艺:手动或自动,室温或加温,完全固化时间、混合后胶的凝固时间等;
3)成本:灌封材料的比重差别很大,我们一定要看灌封后的实际成本,而不要简单的看材料的售价。
用于灌封的胶粘剂按照功能分类有导热灌封胶、粘接灌封胶、防水灌封胶;按照材料分类有聚氨酯灌封胶、有机硅灌封胶和环氧树脂灌封胶,对于选择软胶还是硬胶,其时两种都可以灌封、防水绝缘,如果要求耐高温导热那么建议使用有机硅软胶;如果要求耐低温、那么建议使用有聚氨酯软胶;如果没有什么要求,建议使用环氧硬胶,因为环氧硬胶比有机硅固化时间更快。
环氧树脂灌封胶的应用范围广,技术要求千差万别,品种繁多。从固化条件上分有常温固化和加热固化两类;而从剂型上分双组分和单组分两类,还有就是常温固化环氧灌封胶一般为双组分的,它的优势在于灌封后不需加热即可固化,对设备要求不高,使用方便,存在的缺陷是胶液混合物作业黏度大,浸渗性差,适用期短,且固化物的耐热性和电性能不是很高,一般多用于低压电子器件的灌封或不宜加热固化的场合使用。
五、灌封工艺
灌封产品的质量,主要与产品设计、元件选择、组装及所用灌封材料密切相关,灌封工艺也是不容忽视的因素。环氧灌封有常态和真空两种灌封工艺。
环氧树脂.胺类常温固化灌封料,一般用于低压电器,多采用常态灌封。
环氧树脂.酸酐加热固化灌封料,一般用于高压电子器件灌封,多采用真空灌封工艺。
目前常见的有手工真空灌封和机械真空灌封两种方式,而机械真空灌封又可分为A、B组分先混合脱泡后灌封和先分别脱泡后混合灌封两种情况。
其操作方法有三种:
第一种:单组份电子灌封胶,直接使用,可以用抢打也可以直接灌注;
第二种:双组份缩合型电子灌封胶,固化剂2%-3%或其他比例,搅拌-抽真空脱泡-灌注;
第三种:加成型电子灌封胶,固化剂1:1、10:1;
工艺流程如下:
(1)手工真空灌封工艺
(2)机械真空灌封工艺
1)计量:准确称量A组分和B组分(固化剂)。
2)混合:混合各组份;
3)脱泡:自然脱泡和真空脱泡;
4)灌注:应在操作时间内将胶料灌注完毕否则影响流平;
5)固化:加温或室温固化,灌封好的产品置于室温下固化,初固后可进入下道工序, 完全固化需8~24小时。夏季温度高,固化会快一些;冬季温度低,固化会慢一些。
(3)注意事项:
a、被灌封产品的表面在灌封前必须加以清洁!
b、注意在称量前,将 A 、B 组份分别充分搅拌均匀,使沉入底部的颜料(或填料)分散到胶液中。
c、底涂不可与胶料直接混合,应先使用底涂,待底涂干后,再用本胶料灌封。
d、胶料的固化速度与温度有一定的关系,温度低固化会慢一些。
相比之下,机械真空灌封,设备投资大,维护费用高,但在产品的一致性、可靠性等方面明显优于手工真空灌封工艺。无论何种灌封方式,都应严格遵守设定的工艺条件,否则很难得到满意的产品。
六、灌封产品常出现的问题及原因分析
(1)局部放电起始电压低,线间打火或击穿电视机、显示器输出变压器,汽车、摩托车点火器等高压电子产品,常因灌封工艺不当,工作时会出现局部放电(电弧)、线间打火或击穿现象,是因为这类产品高压线圈线径很小,一般只有0.02~0.04mm,灌封料未能完全浸透匝间,使线圈匝间存留空隙。由于空隙介电常数远小于环氧灌封料,在交变高压条件下,会产生不均匀电场,引起界面局部放电,使材料老化分解,引起绝缘破坏。
从工艺角度分析,造成线间空隙有以下两方面原因:
1)灌封时真空度不够高,间空气未能完全排除,使材料无法完全浸渗。
2)灌封前胶水或产品预热温度不够,黏度不能迅速降低,影响浸渗。 对于手工灌封或先混合脱泡后真空灌封工艺,物料混合脱泡温度高、作业时间长或超过物料适用期,以及灌封后产品未及时进入加热固化程序,都会造成物料黏度增大,影响对线圈的浸渗。先前据有关专家介绍,热固化环氧灌封材料复合物,起始温度越高,黏度越小,随时间延长,黏度增长也越迅速。因此为使物料对线圈有良好的浸渗性,操作上应注意如下几点:
1)灌封料复合物应保持在给定的温度范围内,并在适用期内使用完毕。
2)灌封前,产品要加热到规定温度,灌封完毕应及时进入加热固化程序。
3)灌封真空度要符合技术规范要求。
(2)灌封件表面缩孔、局部凹陷、开裂灌封料在加热固化过程中,会产生两种收缩,即由液态到固态相变过程中的化学收缩和降温过程中的物理收缩。进一步分析,固化过程中的化学变化收缩又有两个过程,从灌封后加热化学交联反应开始到微观网状结构初步形成阶段产生的收缩,我们称之为凝胶预固化收缩。从凝胶到完全固化阶段产生的收缩我们称之为后固化收缩。这两个过程的收缩量是不一样的。前者由液态转变成网状结构过程中,物理状态发生突变,反应基团消耗量大于后者,体积收缩量也高于后者。凝胶预固化阶段(75℃/3h)环氧基消失大于后固化阶段(110℃/3h),差热分析结果也证明这点,试样经750℃/3h处理后其固化度为53%。
若我们对灌封产品的采取一次高温固化,则固化过程中的两个阶段过于接近,凝胶预固化和后固化近乎同时完成,这不仅会引起过高的放热峰,损坏元件,还会使灌封件产生巨大的内应力,造成产品内部和外观的缺损。为获得良好的产品,我们必须在灌封料配方设计和固化工艺制定时,重点关注灌封料的固化速度(即A、B复合物凝胶时间)与固化条件的匹配问题。通常采用的方法是:依照灌封料的性质、用途按不同温区分段固化的工艺。据专家介绍,彩色电视机输出变压器灌封按不同温区分段固化规程及产品内部放热曲线。在凝胶预固化温区段灌封料固化反应缓慢进行,反应热逐渐释放,物料黏度增加和体积收缩平缓进行。此阶段物料处于流态,则体积收缩表现为液面下降,直至凝胶,可完全消除该阶段体积收缩内应力。从凝胶预固化到后固化阶段,升温也应平缓,固化完毕,灌封件应随加热设备同步缓慢降温,多方面减少、调节产品内应力分布状况,可避免产品表面产生缩孔、凹陷甚至开裂现象。
对灌封料固化条件的制订,还要参照灌封产品内封埋元件的排布、饱满程度及产品大小、形状、单只灌封量等。对单只灌封量较大而封埋元件较少的,适当地降低凝胶预固化温度并延长时间是完全必要的。
(3)固化物表面不良或局部不固化这些现象也多与固化工艺相关。主要原因是:
1)计量或混合装置失灵、生产人员操作失误。
2)A组分长时间存放出现沉淀,用前未能充分搅拌均匀,造成树脂和固化剂实际比例失调。
3)B组分长时间敞口存放、吸湿失效。
4)高潮湿季节灌封件未及时进入固化程序,物件表面吸湿。
总之,要获得一个良好的灌封产品,灌封及固化工艺的确是一个值得高度重视的问题。
电子灌胶常见问题
1)电子灌封胶中毒不固化如何解决?
硅胶中毒一般发生在加成型电子灌封胶上,中毒后硅胶会出现不固化的现象,所以使用加成型灌封胶时应避免与含磷、硫、氮的有机化合物接触,或与加成型硅胶同时使用聚氨酯、环氧树脂、不饱和聚脂、缩合型室温硫化硅橡胶等产品,防止发生中毒不固化现象。
2)不小心粘到的电子灌封胶用什么可以清洗干净?
常用的硅胶清洗剂主要有酒精、丙酮、白酒等等,记得在用时都要稀释涂。
3)冬天电子灌封胶干不了怎么办?
由于冬天气温很低,造成电子灌封胶在混合后固化很慢甚至长时间不固化,所以我们可以提高固化的温度,可以将灌好胶的产品放在25℃烘箱里固化。
环氧树脂灌封料及其工艺和常见问题
1、在电子封装技术领域曾经出现过两次重大的变革。
第一次变革出现在20世纪70年代前半期,其特征是由针脚插入式安装技术(如DIP)过渡到四边扁平封装的表面贴装技术(如QFP);第二次转变发生在20世纪90年代中期,其标志是焊球阵列,BGA型封装的出现,与此对应的表面贴装技术与半导体集成电路技术一起跨人21世纪。随着技术的发展,出现了许多新的封装技术和封装形式,如芯片直接粘接、灌封式塑料焊球阵列(CD-PBGA)、倒装片塑料焊球阵列(Fc-PBGA)、芯片尺寸封装(CSP)以及多芯片组件(MCM)等,在这些封装中,有相当一部分使用了液体环氧材料封装技术。灌封,就是将液态环氧树脂复合物用机械或手工方式灌入装有电子元件、线路的器件内,在常温或加热条件下固化成为性能优异的热同性高分子绝缘材料。
2、产品性能要求
灌封料应满足如下基本要求:性能好,适用期长,适合大批量自动生产线作业;黏度小,浸渗性强,可充满元件和线间;在灌封和固化过程中,填充剂等粉体组分沉降小,不分层;固化放热峰低,固化收缩小;固化物电气性能和力学性能优异,耐热性好,对多种材料有良好的粘接性,吸水性和线膨胀系数小;在某些场合还要求灌封料具有难燃、耐候、导热、耐高低温交变等性能。
在具体的半导体封装中,由于材料要与芯片、基板直接接触,除满足上述要求外,还要求产品必须具有与芯片装片材料相同的纯度。在倒装芯片的灌封中,由于芯片与基板间的间隙很小,要求灌封料的黏度极低。为了减少芯片与封装材料间产生的应力,封装材料的模量不能太高。而且为了防止界面处水分渗透,封装材料与芯片、基板之间应具有很好的粘接性能。
3、灌封料的主要组份及作用
灌封料的作用是强化电子器件的整体性,提高对外来冲击、震动的抵抗力;提高内部元件、线路间绝缘,有利于器件小型化、轻量化;避免元件、线路直接暴露,改善器件的防水、防潮性能。
环氧树脂灌封料是一多组分的复合体系,树脂、固化剂、增韧剂、填充剂等组成,对于该体系的黏度、反应活性、使用期、放热量等都需要在配方、工艺、铸件尺寸结构等方面作全面的设计,做到综合平衡。
3.1 环氧树脂
环氧树脂灌封料一般采用低分子液态双酚A型环氧树脂,这种树脂黏度较小,环氧值高。常用的有E-54、E-51、E-44、E-42。在倒装芯片下填充的灌封中,由于芯片与基板之间的间隙很小,因此要求液体封装料的黏度极低。故单独使用双酚A型环氧树脂不能满足产品要求。为了降低产品黏度,达到产品性能要求,我们可以采用组合树脂:如加入黏度低的双酚F型环氧树脂、缩水甘油酯型树脂以及具有较高耐热、电绝缘性和耐候性的树脂环族环氧化物。其中,树脂环族环氧化物本身还具有活性稀释剂的作用。
3.2 固化剂
固化剂是环氧灌封料配方中的重要成分,固化物性能很大程度取决于固化剂的结构。
(1)室温固化一般采用脂肪族多元胺做固化剂,但这类固化剂毒性大、刺激性强、放热激烈,固化和使用过程易氧化。因此,需要对多元胺进行改性,如利用多冗胺胺基上的活泼氢,部分与环氧基合成为羟烷基化及部分与丙烯晴合成为氰乙基化的综合改性,可使固化剂达到低黏度、低毒、低熔点、室温固化并有一定韧性的综合改性效果。
(2)酸酐类固化剂是双组分加热固化环氧灌封料最重要的固化剂。常用的固化剂有液体甲基四氢邻苯二甲酸酐、液体甲基六氢邻苯二甲酸酐、六氢邻苯二甲
酸酐、甲基纳迪克酸酐等。这类固化剂黏度小,配合用量大,能在灌封料配方中起到固化、稀释双重作用,固化放热缓和,固化物综合性能优异。
3.3固化促进剂
双组分环氧一酸酐灌封料,一般要在140℃左右长时间加热才能固化。这样的固化条件,不仅造成能源浪费,而且多数电子器件中的元件、骨架外壳是难以承受的。配方中加入促进剂组分则可有效降低固化温度、缩短固化时间。常用的促进剂有:卞基二胺、DMP-30等叔胺类。也可使用咪唑类化合物和羧酸的金属盐,如2-乙基-4-甲基咪唑、2-甲基咪唑等。
3.4偶联剂
为了增加二氧化硅和环氧树脂之间的密着性,需加入硅烷偶联剂。偶联剂可以改善材料的粘接性和防潮性。适用于环氧树脂的常用硅烷偶联剂有缩水甘油氧、丙基三氧基硅烷(KH-560)、苯胺基甲三乙氧基硅烷、α-氯代丙基三甲氧基硅烷、α-巯基丙基三甲氧基硅烷、苯胺甲基三甲氧基硅烷、二乙烯二胺基丙基三甲氧基硅烷等。
3.5 活性稀释剂
单独使用环氧树脂,加入无机填料后黏度明显增大,不利于操作和消泡,常需加入一定量的稀释剂,以增加其流动性和渗透性,并延长使用期,稀释剂有活性和非活性之分。非活性稀释剂不参与固化反应,加入量过多,易造成产品收缩率提高,降低产品力学性能及热变形。活性稀释剂参与固化反应增加了反应物的粘性,对固化物性能影响较小。灌封料中选用的就是活性稀释剂,常用的有:正丁基缩水甘油醚、烯丙基缩水甘油醚、二乙基己基缩水甘油醚、苯基缩水甘油醚。
3.6 填充剂
灌封料中填料的加入对提高环氧树脂制品的某些物理性能和降低成本有明显的作用。它的添加不仅能降低成本,还能降低固化物的热膨胀系数、收缩率以及增加热导率。在环氧灌封料中常用的填充剂有二氧化硅、氧化铝、氮化硅、氮化硼等材料。二氧化硅又分为结晶型、熔融角型和球形二氧化硅。在电子封装用灌封料中,由于产品要求,优选熔融球形二氧化硅。
3.7 消泡剂
为了解决液体封装料固化后表面留有气泡的问题,可加入消泡剂。常用的是乳化硅油类乳化剂。
3.8 增韧剂
增韧剂在灌封料中起着重要作用,环氧树脂的增韧改性主要通过加增韧剂、增塑剂等来改进其韧性,增韧剂有活性和惰性两种,活性增韧剂能和环氧树脂一起参加反应,增加反应物的粘性,从而增加固化物的韧性。一般选择端羧剂液体丁腈橡胶,在体系内形成增韧的"海岛结构",增加材料的冲击韧度和耐热冲击性能。
3.9 其他组分
为满足灌封件特定的技术、工艺要求,还可在配方中加人其他组分。如阻燃剂可提高材料的工艺性;着色剂用以满足产品外观要求等。
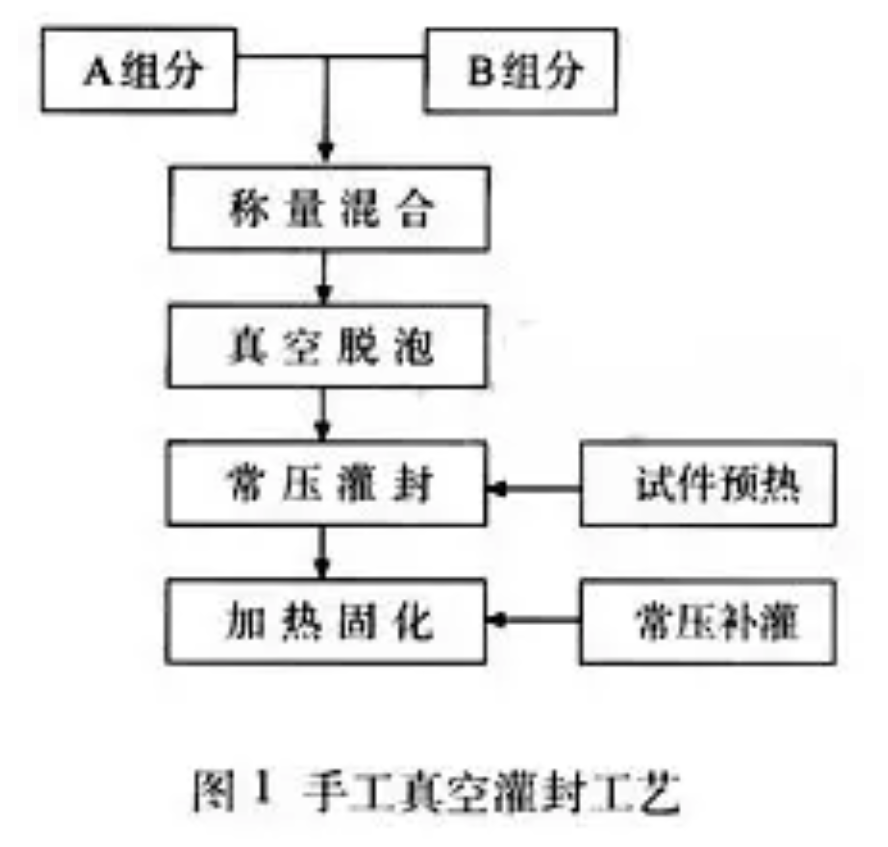
4、灌封工艺
环氧树脂灌封有常态和真空两种工艺。图1为手工真空灌封工艺流程。
5、常见问题及解决方法
5.1 放电、线间打火或击穿现象
由于灌封工艺不当,器件在工作时会产生放电、线间打火或击穿现象,这是因为这类产品高压线圈线径很小(一般只有0.02mm~0.04mm),灌封料未能完全浸透匝间,造成线圈匝问存留空隙。由于空隙介电常数远小于环氧灌封料,在交变高压条件下会产生不均匀电场,引起局部放电,使材料老化分解造成绝缘破坏。从工艺角度来看,造成线间空隙有两方面原因:
(1)灌封时真空度不够高,线问空气未能完全排除,使材料无法完全浸渗;
(2)灌封前产品预热温度不够,灌入产品物料黏度不能迅速降低,影响浸渗。对于手工灌封或先混合脱泡后真空灌封工艺,物料混合脱泡温度高、作业时间长或超过物料适用期以及灌封后产品未及时进入加热固化程序,都会造成物料黏度增大,影响对线圈的浸渗。热同性环氧灌封材料复合物,起始温度越高黏度越小,随时间延长黏度增长也越迅速。因此,为使物料对线圈有良好的浸渗性,操作上应注意做到灌封料复合物应保持在合适的温度范围内,并在适用期内使用完毕。灌封前产品要加热到规定温度,灌封完毕应及时进入加热固化程序,灌封真空度要符合技术规范要求。
5.2 器件表面缩孔、局部凹陷、开裂
灌封料在加热固化过程中会产生两种收缩:由液态到固态相变过程中的化学收缩和降温过程中的物理收缩。固化过程中的化学变化收缩又有两个过程:从灌封后加热化学交联反应开始到微观网状结构初步形成阶段产生的收缩,称之为凝胶预固化收缩;从凝胶到完全固化阶段产生的收缩我们称之为后固化收缩。这两个过程的收缩量是不一样的,前者由液态转变成网状结构过程中物理状态发生突变,反应基团消耗量大于后者,体积收缩量也高于后者。如灌封产品采取一次高温固化,则固化过程中的两个阶段过于接近,凝胶预固化和后固化近乎同时完成,这不仅会引起过高的放热峰、损坏元件,还会使灌封件产生巨大的内应力造成产品内部和外观的缺损。为获得良好的产品,必须在灌封料配方设计和固化工艺制定时,重点关注灌封料的固化速度与固化条件的匹配问题。通常采用的方法是依照灌封料的性质、用途按不同温区分段固化。在预固化温区段灌封料固化反应缓慢进行、反应热逐渐释放,物料黏度增加和体积收缩平缓进行。此阶段物料处于流态,则体积收缩表现为液面下降直至凝固,可完全消除该阶段体积收缩内应力。从凝胶预固化到后固化阶段升温应平缓,固化完毕灌封件应随加热设备同步缓慢降温,多方面减少、调节产品内应力分布状况,可避免产品表面产生缩孔、凹陷甚至开裂现象。对灌封料固化条件的制订,还要参照灌封器件内元件的排布、饱满程度及产品大小、形状、单只灌封量等。对单只灌封量较大而封埋元件较少的,适当地降低凝胶预固化温度并延长时间是完全必要的。 5.3 固化物表面不良或局部不固化
固化物表面不良或局部不固化等现象也多与固化工艺相关。中国环氧树脂行业协会专家表示,其主要原因是计量或混合装置失灵、生产人员操作失误;A组分长时间存放出现沉淀,用前未能充分搅拌均匀,造成树脂和固化剂实际比例失调,B组分长时间敞口存放,吸湿失效;高潮湿季节灌封件未及时进入固化程序,物件表面吸湿。总之,要获得一个良好的灌封及固化工艺的确是一个值得高度重视的问题。
七、灌封胶施工工艺
1.裂缝标注
检查并标注裂缝的性质 以及裂缝的长度,宽度,深度、走向、贯穿及漏水情况,以便于处理方案。裂缝宽度可用读数显微镜测量,裂缝的深度和走向可用超声、压力或钻孔取样等方法检查。
2.表面处理
对较小的混凝土,混凝土结构的裂缝,用钢丝刷等工具,清除混凝土裂缝,表面的灰尘浮渣及松散层等污物刷器复飞,用酒精或丙酮将原缝两侧2到3厘米范围擦拭干净
3.预埋注胶嘴
在裂缝的交错处、裂缝较宽处及裂缝端部必须设置灌胶嘴,灌胶嘴的间距根据裂缝大小、走向及结构形式而定,一般缝宽0.3~0.5mm时灌胶嘴间距为30~50cm,在一条裂缝上必须设置有进胶、排气或胶口。灌胶嘴可以先用封口胶粘贴在预定位置,也可在封缝时一同粘贴。应特别注意防止堵塞灌胶嘴。
4.封缝胶封缝
封缝质量的好坏直接影响灌胶效果与质量,应特别予以重视。裂缝的封闭按推荐配胶比例称取并调配封口胶,用油灰刀沿裂缝往复涂刮后均匀涂抹一层厚约1~2mm、宽2~3cm的胶泥,注意防止小气泡及密封不严。
5.封缝检验
一般情况下,在使用封口胶封缝后1~2天即可进行试漏检验,检验裂缝的密封效果及贯通情况。若用压缩空气进行试漏实验,可沿裂缝涂刷一层肥皂水从灌胶嘴吹入压缩空气(压力与灌胶压力相同),漏气处可再行封闭;若用压力水进行试漏试验,检验完毕后应该压缩空气吹净积水,并留有足够的时间让裂缝干燥。对重要 构件或走向复杂的裂缝,建议进行试漏检验,以确保注胶效果。
6 配制灌封胶
配制裂缝灌注胶液前应将甲、乙(A/B)两组分充分摇匀,根据估计的灌胶量按推荐配胶比准确称量两组分,并混合均匀。从胶液混合开始,注胶操作应在胶液适用期内完成(25°C时约为60分钟)
7.低压低速灌胶
注胶操作应使用专用的注胶器具。注胶前,应用压缩空气将缝吹净,达到无水干燥状态。根据裂缝区域大小,可采用单孔灌胶或分区群孔灌胶。在一条裂缝上的灌胶可有浅到深,由下到上,由一端到另外一端。灌胶压力常采用0.2MPa,在保证灌胶顺畅的情况下,采用较低的灌胶压力和较长的灌胶时间,可以获得更好的灌胶效果。当最后一个出胶口出胶且出胶速率保持稳定后,再保持压注10分钟左右即可停止灌胶。拆除管路,并注意防止流胶。
8.胶液固化
卡本灌封胶一般理论条件下在5°C以上的环境中固化,具体固化时间视环境温度而定。一般情况(25°C)下固化2~3天即可。
9、灌胶效果检验
灌胶结束后应检验灌胶效果及质量,凡有不密实等不合格情况,应进行补注。灌胶效果一般可采用压水检查(气密测试),在裂缝较多、灌胶质量较差的部位设置检查孔,水压值一般在灌胶压力的70~80%,基本不吸水不渗漏即可认为合格。对大型构件,还可选择适当部位进行钻芯取样检查,并可将芯样加工成试件进行力学性能试验。
八、双组份灌胶工艺案例
需要胶水封入壳体和线路板
灌胶步骤1:首先在空壳子里面灌封胶
空壳子灌满三分之一
灌胶步骤2:将线路板压入灌好胶的盒子中
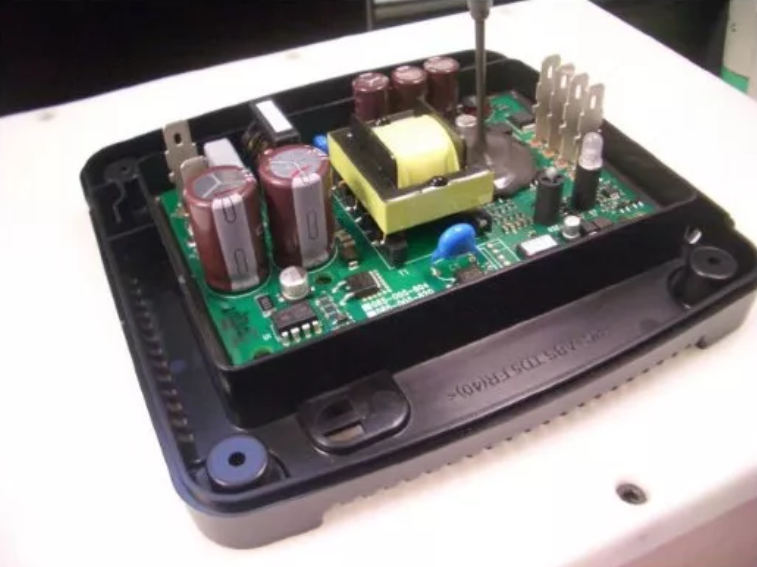
灌胶步骤3:将压入线路板的盒子继续灌胶
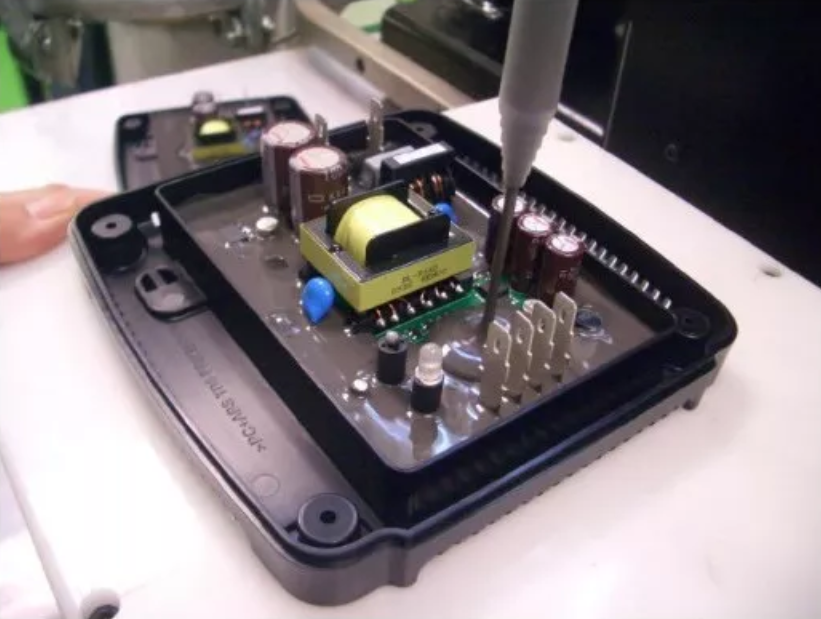
将胶水均衡灌平
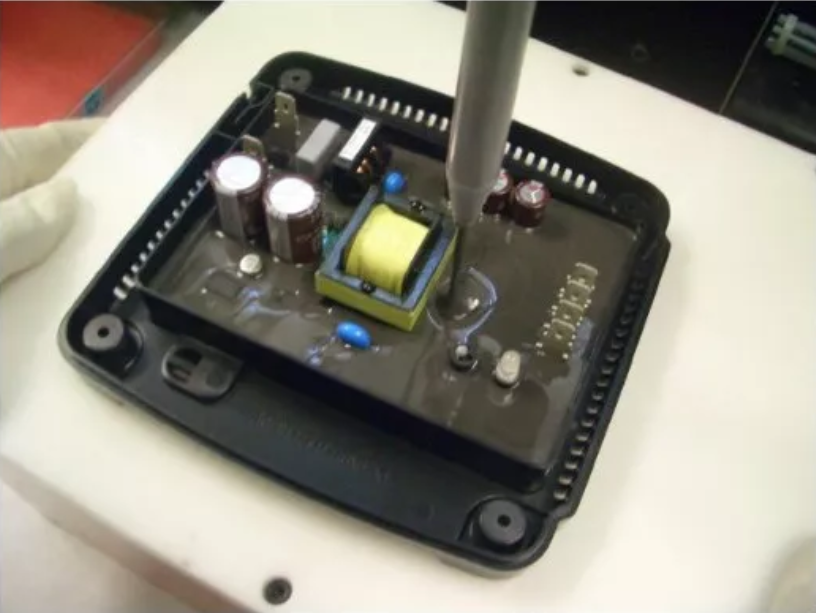
继续均衡灌胶

灌满壳体
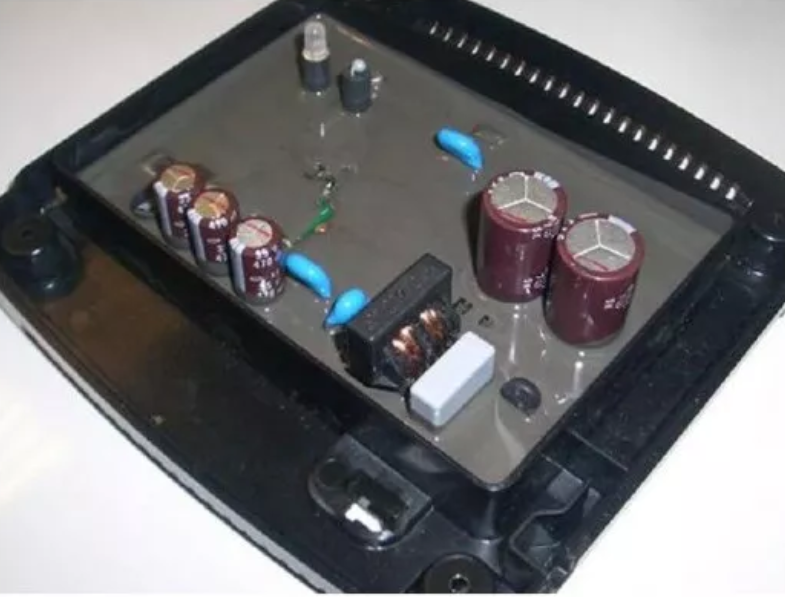
完成灌胶
九、PCBA灌胶的三种方法
1、半自动灌胶机
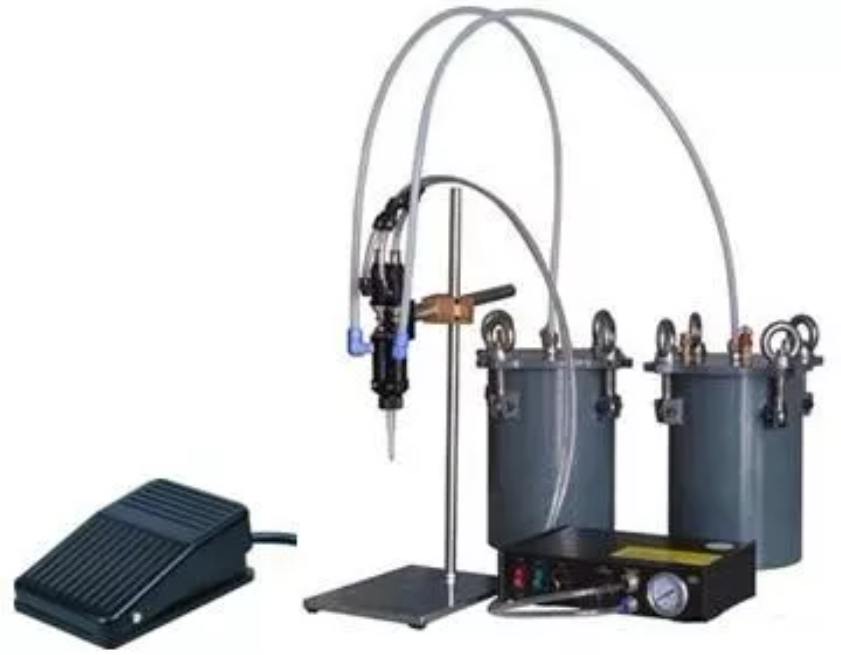
在给产品灌胶时,放在流水线旁,人工将产品放入出胶头下方,按启动开关,机器便自动灌胶,灌胶完毕自动停止。然后操作人员再将灌好胶的产品放到流水线上即可,半自动灌胶机适合于各类PCBA产品,不论大小。
2、自动灌胶机
如果都以小产品居多,灌胶方式也很简单,将产品放入一个治具中,然后将治具放到灌胶机的台面上,按一下启动,机器便开始灌胶,等所有灌胶完毕之后,自动停止,然后操作人员将治具从台面上取下,然后放上另一个装好产品的治具,按下启动,以此循环,操作人员要做的就是放治具,按启动按钮。
3、全自动灌胶线
将装有产品的治具放到传输线上,机器自动灌胶,自动送料到烤箱过炉,节省人工,高效运转。 以上就是自动灌胶的3种方法,自动灌胶设备的使用可以更好的节省人工,提高生产效率。
来源:图文综合整理自网络
|